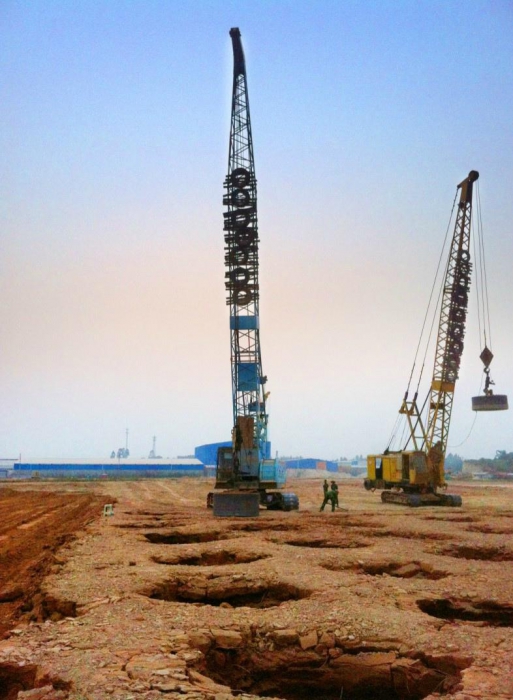
水泥粉喷桩地基加固施工突出点?
1、施钻前应进行放线,准确定出各孔位中心,打木桩作出标记,并在木桩周转撒上石灰以醒目,便于施钻过程中寻找。
软基工程多数情况是有局部地段地质情况和原来设计不同,出现局部地基承载力达不到设计要求,或者由于局部地段含水量过大(原有排水系统不畅,原有地基土质渗水性不好)造成地基软弹(翻浆,弹簧土地段)。
2、所有桩在制桩过程中,都必须准确测量钻进深度,确保桩顶及桩底标高符合设计要求。
3、桩体顶端一般常因喷粉量不足、搅拌不匀等原因(Reason)造成质量缺陷,因此粉体的喷射长度应比设计桩顶标高高出40cm~50cm,待桩体达到一定强度(strength)(一般可取25d~30d)后,再将多余桩体截掉。此时应注意采用合适的截断方法,避免保留桩体遭到破坏。截掉桩头时应谨慎操作控制,先用人工沿周连凿槽,再用铁锤轻轻击碎,任何情况下都不得采用猛力冲击(chōng jī)的方式来切断(割开;截断)桩头。条件(tiáo jiàn)允许时,应采用有效的切割工具实施桩头截除。为避免桩顶因送气压力(pressure)骤减出现松散段,在每根桩的上部1m的范围(fàn wéi)内,应重复钻进喷粉一次。
4、采用喷桩加固的建筑物基础底下均应设置有一定厚度的垫层,以均匀传递上部荷载。制桩时,必须按设计要求将桩顶嵌入到垫层中,这是保证桩基的整体性所必须的。因此,施工时,桩顶预留50cm,以确保桩头质量。
5、粉喷适宜在含有地下水的土层中施工,但在任何情况钻进和制作桩过程(guò chéng)中,均不得随意向孔中注水;对特别干燥(缺乏水分)的土层,可经试验(test)论证后,提前向土层中注水或浸水湿润,并等水分均匀掺透到土层中后,再实施制桩。基坑支护工程根据基坑的深度把基坑支护工程分为两种:浅基坑支护工程和深基坑支护工程
6、必须做到粉体喷出量试验,保证按设计(Design)规定的掺入比向孔中喷射粉料,不允许降低(reduce)喷入量。
7、严格防止地下水或其他水渗入套管等输送(transport)气粉混合料的通道中,以免堵塞通道,影响喷粉质量。防止方法是钻头一入土就不停地送气。假若造成堵塞,则应起升钻杆,拆下钻头,用铅(外观:带蓝色的银白色)丝通开。
8、向固化剂罐中送料时,应在罐口装过滤网,防止纸屑、灰块、杂物、金属碴等掉进罐内。
9、钻架必须注意(attention)保持竖直,以保证桩体的垂直度。每一孔在开钻前,均须检查钻头是否对准桩位中心,不得偏位。
10、制桩过程中要时刻注意施工情况,避免发生供气不足、喷粉不够、断喷、喷嘴堵塞等不良(bù líang)现象(phenomenon),发现问题应及时处理。
11、每根桩的桩体制作应一气呵成,不得在喷粉过程中间歇中断。应根据桩长和固化料掺入比计算出一根桩的喷灰量,并装入灰罐,完成一根桩后,再装入另一根桩的用灰。当然,每根桩的用灰入罐量应稍高于计算用量,以防因喷灰不均匀造成贮灰量不足。
12、桩体强度(strength)除与掺入料有直接关系外,还与土层的物理力学性质密切相关,施工时应充分结合土层的含水量、粘土粒含量、密度、压缩系数、塑性指数、松散程度、抗剪指标、土层厚度、地下水埋深度等,合理确定钻进速度、提升钻头速度、成桩时间、掺入料用量(dosage),以达到最佳的成桩效果。
13、钻孔时应把握钻进速度,不宜过快,确保使原位土搅拌后疏松透气。软基工程多数情况是有局部地段地质情况和原来设计不同,出现局部地基承载力达不到设计要求,或者由于局部地段含水量过大(原有排水系统不畅,原有地基土质渗水性不好)造成地基软弹(翻浆,弹簧土地段)。提升外头时应均匀慢速,保证掺入料与原位土充分混合。严格控制固化剂喷入量,固化剂喷入量与设计值误差应控制在3%之内。
14、粉喷桩应自然养护14d以上始可进行基坑开挖。为防止(fáng zhǐ)开挖作业中造成桩顶损坏,应采用人工开挖和出土;当挖除土层很厚时,桩顶以上80cm以上部分可用机械开挖。
15、施工结束后应开挖基槽对所有桩进行质量(Mass)检测及复合地基(dì jī)承载力检测,必要时还应进行单桩承载力和桩体强度检测。所有检测指标必须达到设计标准,桩位及桩数也必须符合设计要求(demand)。
16、对断桩、缺桩、缩颈、逊径、强度较低、桩长不够、偏位较大、表面缺陷等事故(accident),必须按设计要求进行补强处理,不允许降低(reduce)设计标准。
17、施工过程中应有专人负责记录所在粉喷桩的桩号、成桩时间、设计桩长、实际桩长、设计桩径、实际桩径、固化剂实际喷入量、桩顶标高等。成桩时间记录必须按制桩程序(钻进、提升、复搅)详细(xiáng xì)记载,时间记录偏差不得大于5s,桩长(孔深)记录误差不得大于5cm.
以上网站内容均根据学员实际工作中遇到的问题整理而成,供参考,如有问题请及时沟通、指正。